Are Hydraulics and Pneumatics Considered in the Machine Safety Cycle?
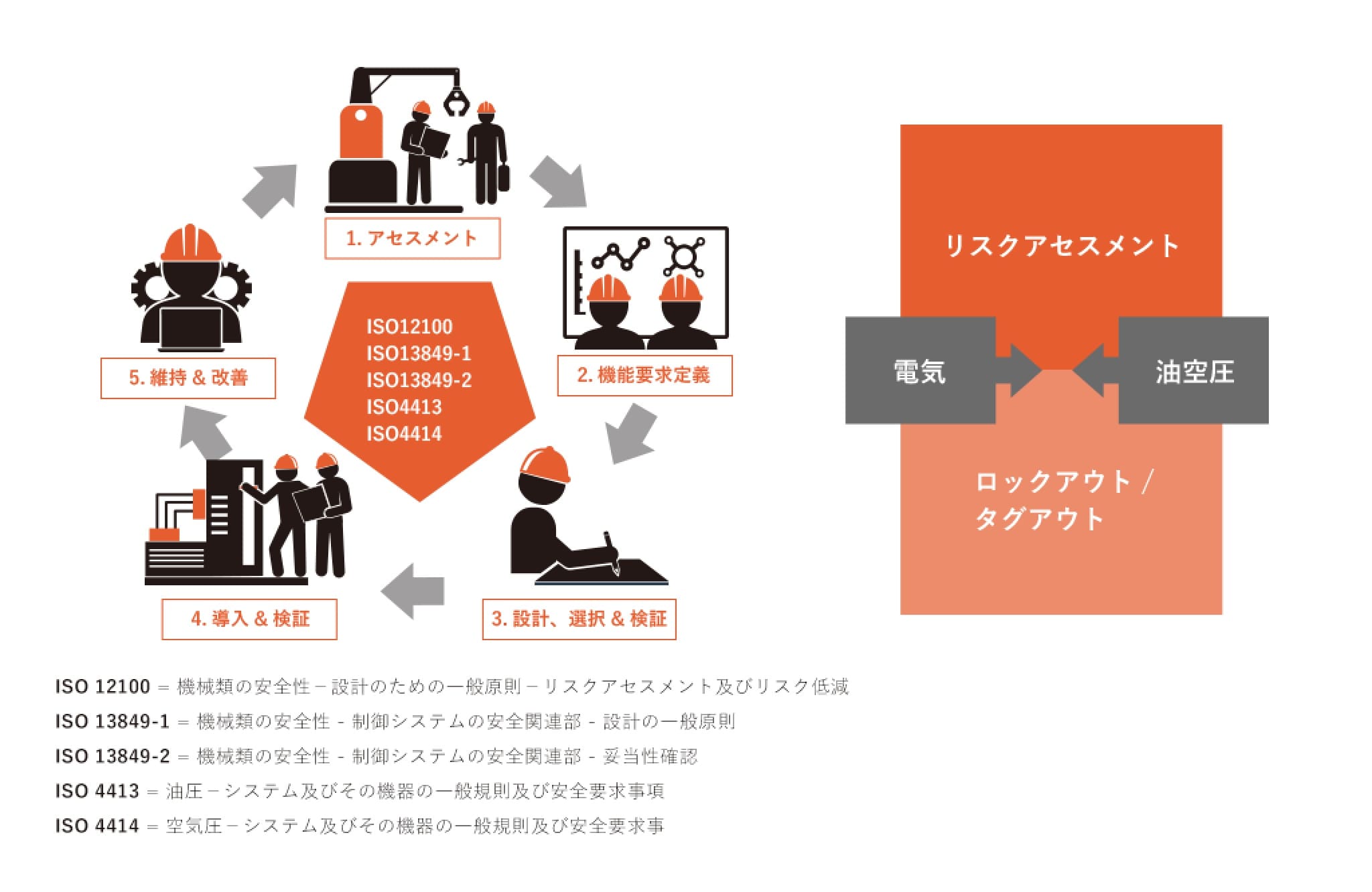
What is Machine Safety?
Machine accidents account for about one-fifth of occupational accidents, and the number of fatalities is the second highest after falls, and the number of occupational accidents due to machine accidents has been increasing in recent years. This trend is expected to continue in the future as production facilities become more sophisticated, machinery and equipment become more energy efficient, and workers diversify, against the backdrop of improved productivity.
Mechanical accidents are characterized by a high degree of bodily injury, and are likely to lead to fatal accidents and accidents that leave aftereffects. Accidents such as being hit, caught in something, cut, or scraped can be prevented by implementing appropriate risk assessment at the stage of machine specification design.
“Safe” in machine safety is defined as “free from acceptable risk”. (ISO/IEC Guide 51:1999) “Absolute safety” does not exist, Based on the premise that people make mistakes and machines break down, there is a demand for machine design that protects the safety of workers even if a person makes a mistake or the machine itself breaks down.
The importance of safety education for people (workers), such as calling attention to work and proper use of protective equipment, will not change in the future. However, while safety education is widely implemented from the perspective of preventing occupational accidents, regarding the “safety of machines themselves”, the government has created “Guidelines for Comprehensive Safety Standards for Machinery” and the “industrial Safety and Health Law”. Although it is stipulated in the revision of Article 28-2 (Risk Assessment Regulations), its dissemination and efforts themselves are not sufficient.
Machines are production equipment operated by various power sources. In addition to electrical control, there are countless hydraulic and pneumatic equipment in factories, but the current situation in Japan is that the risk assessment of hydraulic and pneumatic equipment is completely overlooked.
Machinery Definition
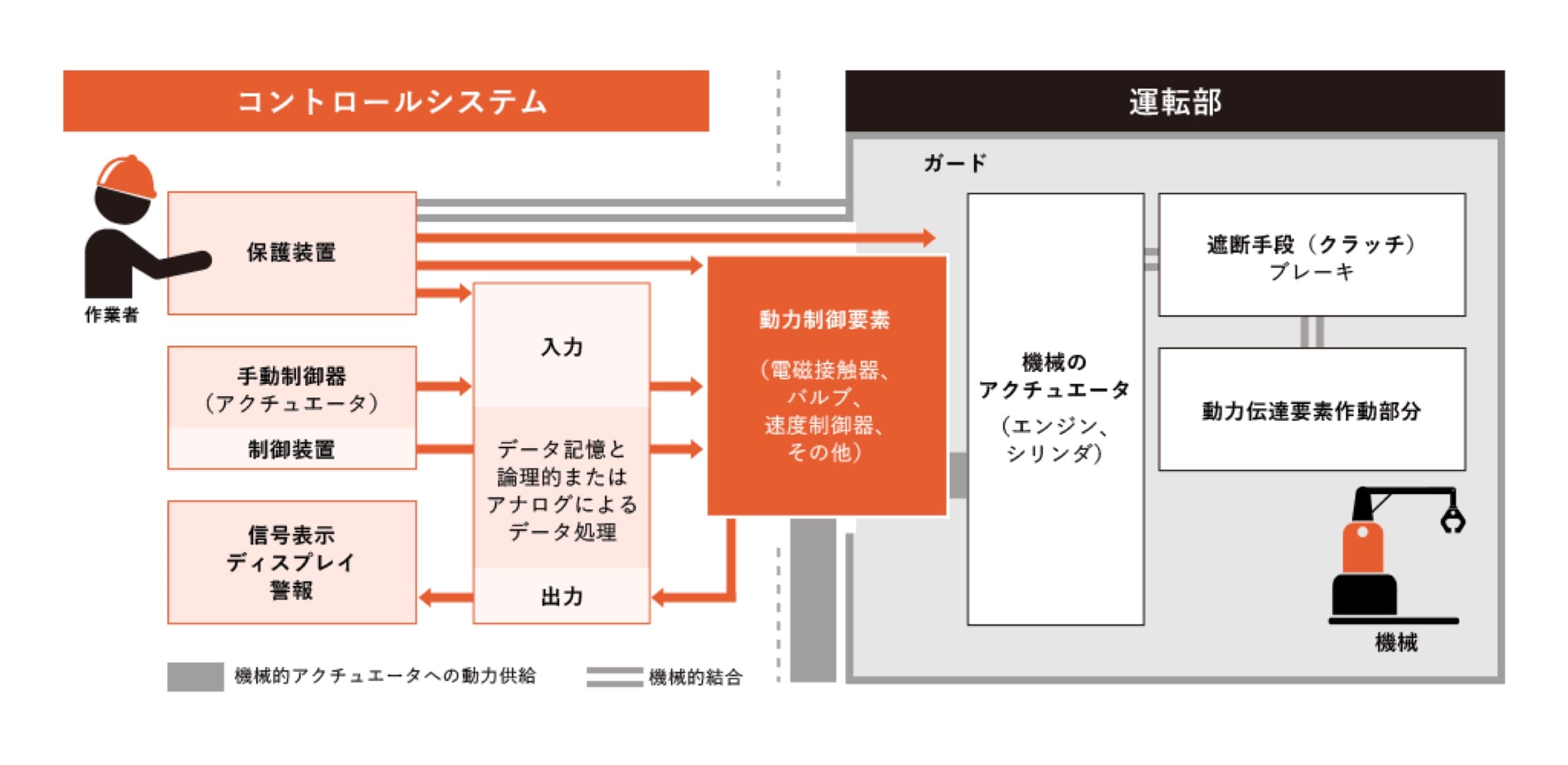
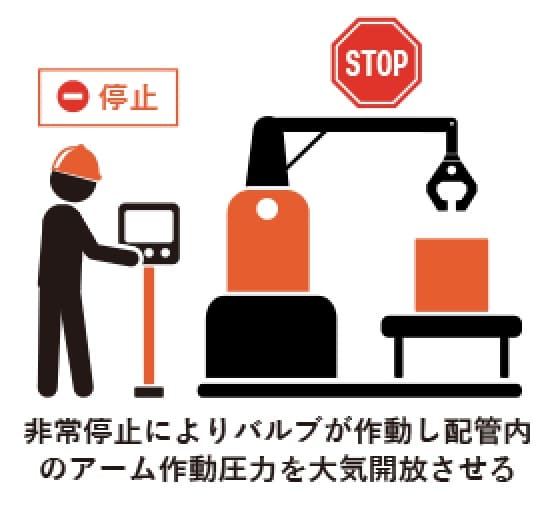
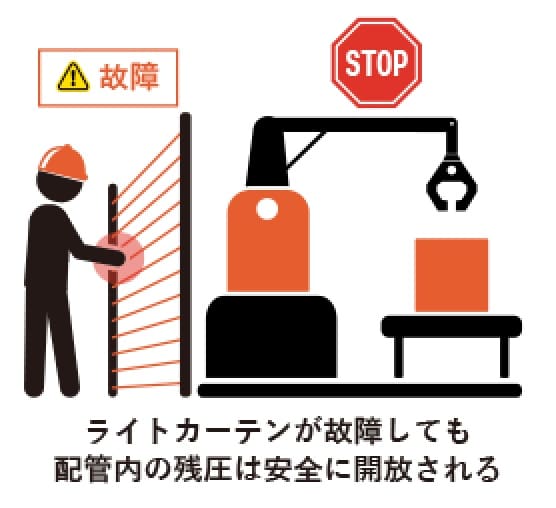
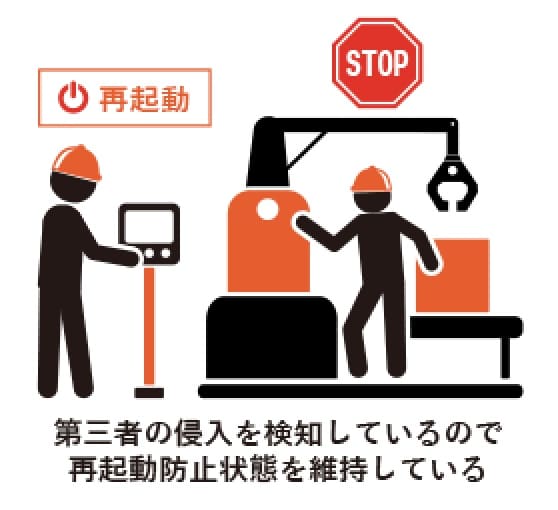
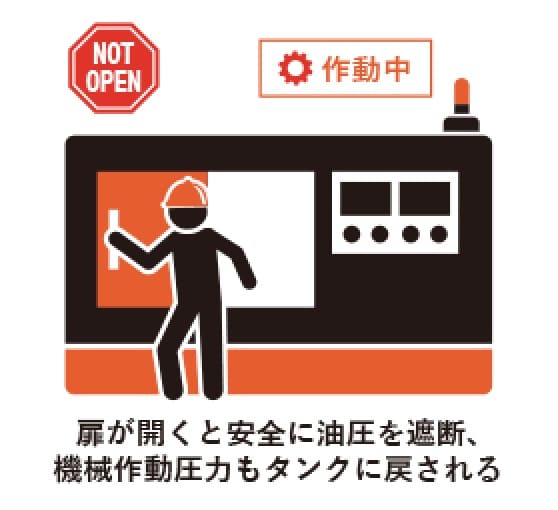
Effect of Investment by Efforts for Machine Safety
Investing in establishing a positive safety culture and using modern methods and technologies contribute significantly to profits and OEE (availability, production speed, and quality).
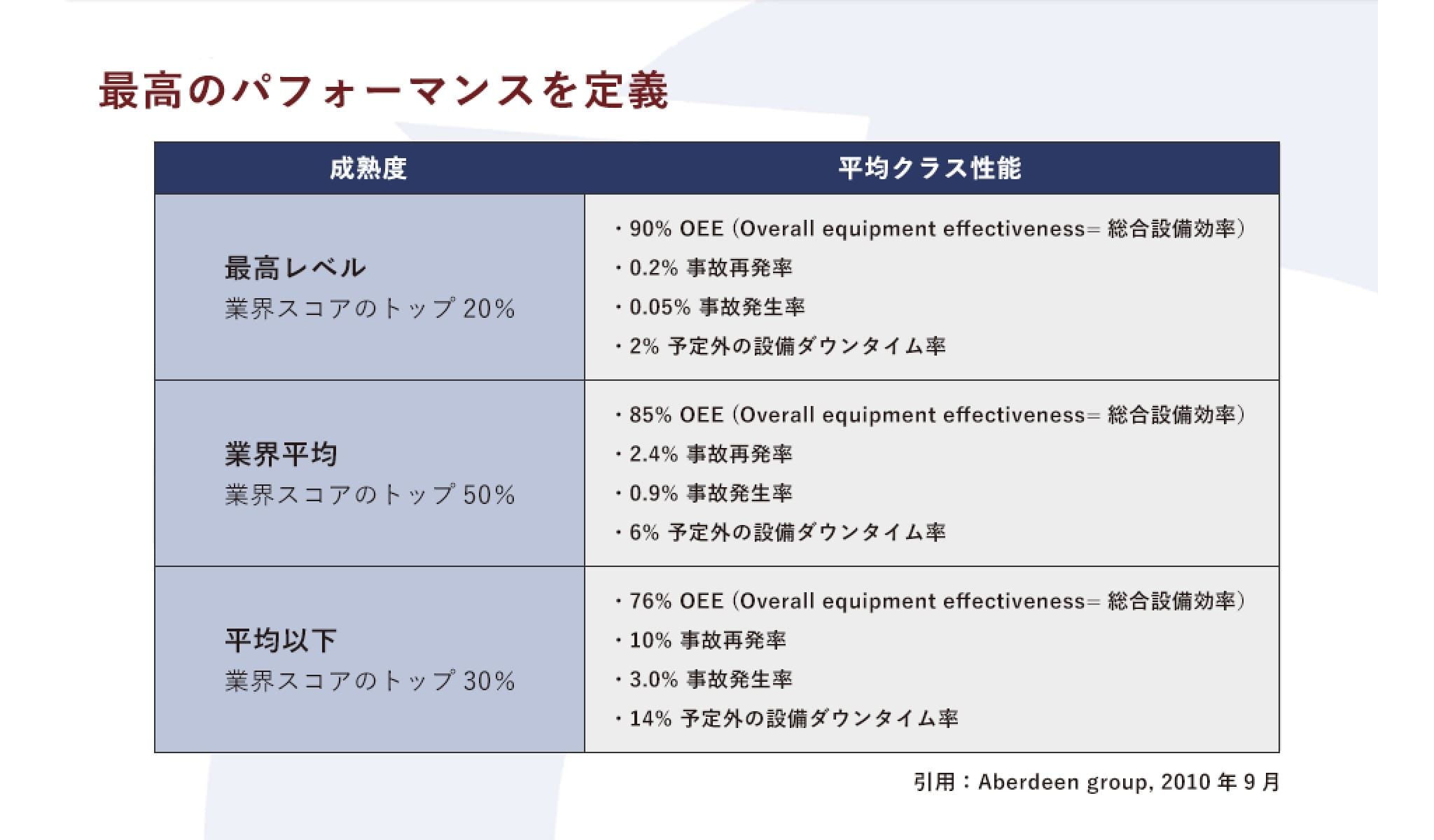
Hydraulic and Pneumatic Machine Safety and Occupational Safety Solutions ISO13849-1 (Category/Performance Level)
Hydraulic Safety Valve System
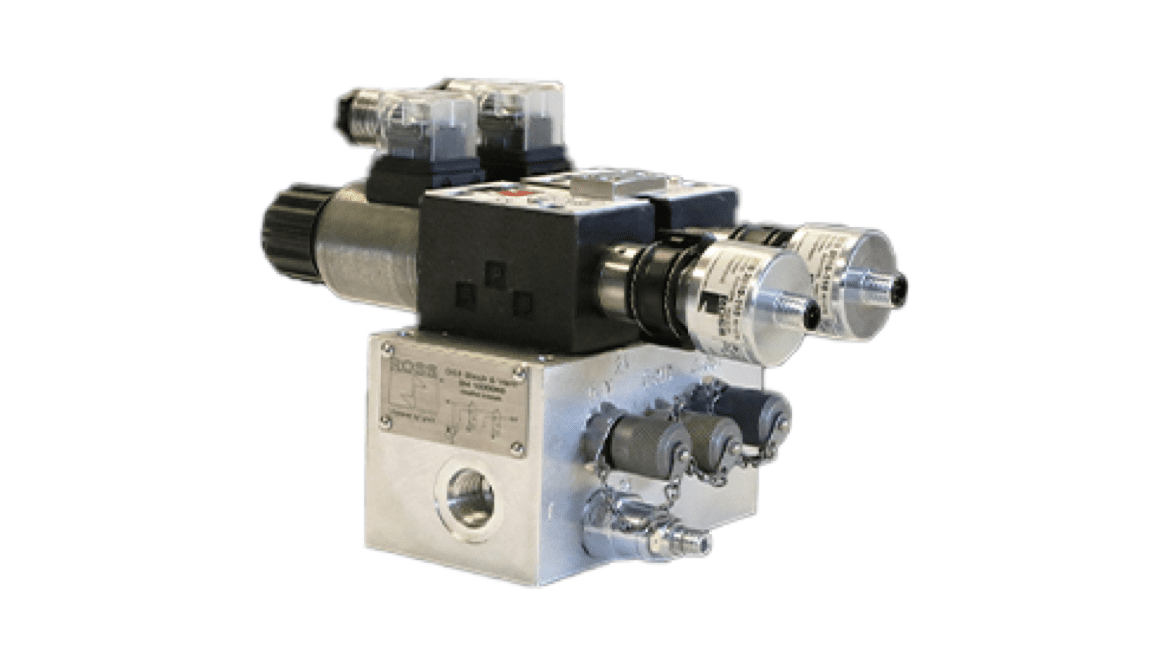
Safety shut-off/tank return valve
- Redundant valve system
- With relief valve
- Mechanism to prevent tampering
- Maximum flow rate: about 189L/m
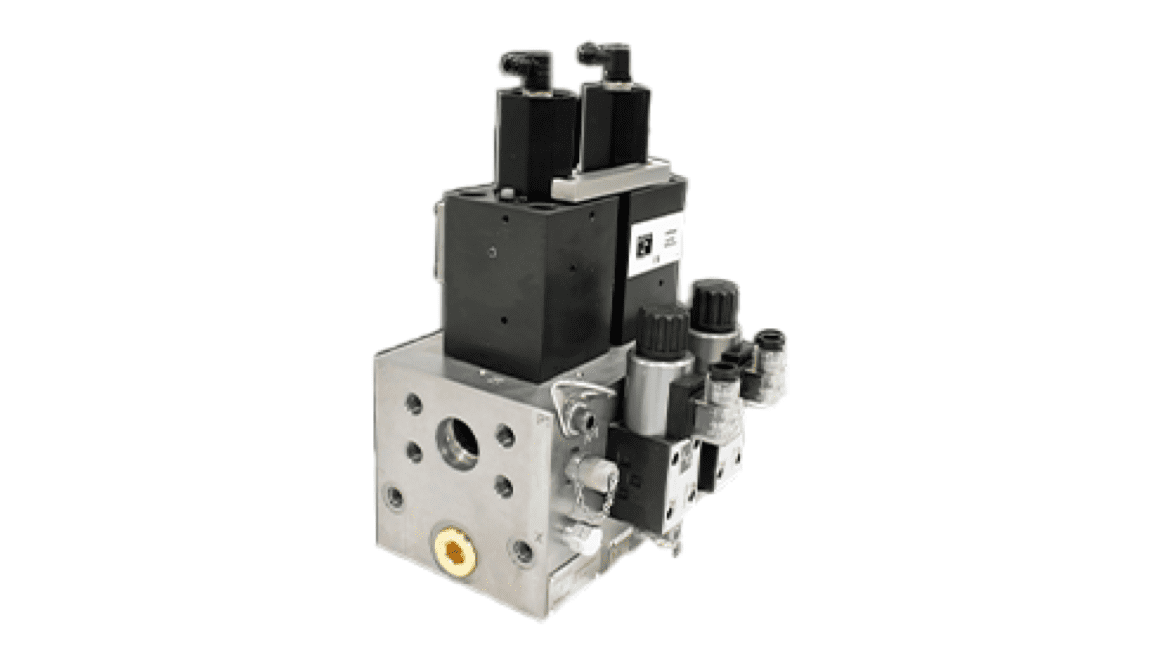
Safety shut-off/holding valve
- Redundant valve system
- Vertical load retention during power failure
- Mechanism to prevent tampering
- Maximum flow rate: about 548L/min
Pneumatic Safety Valve System
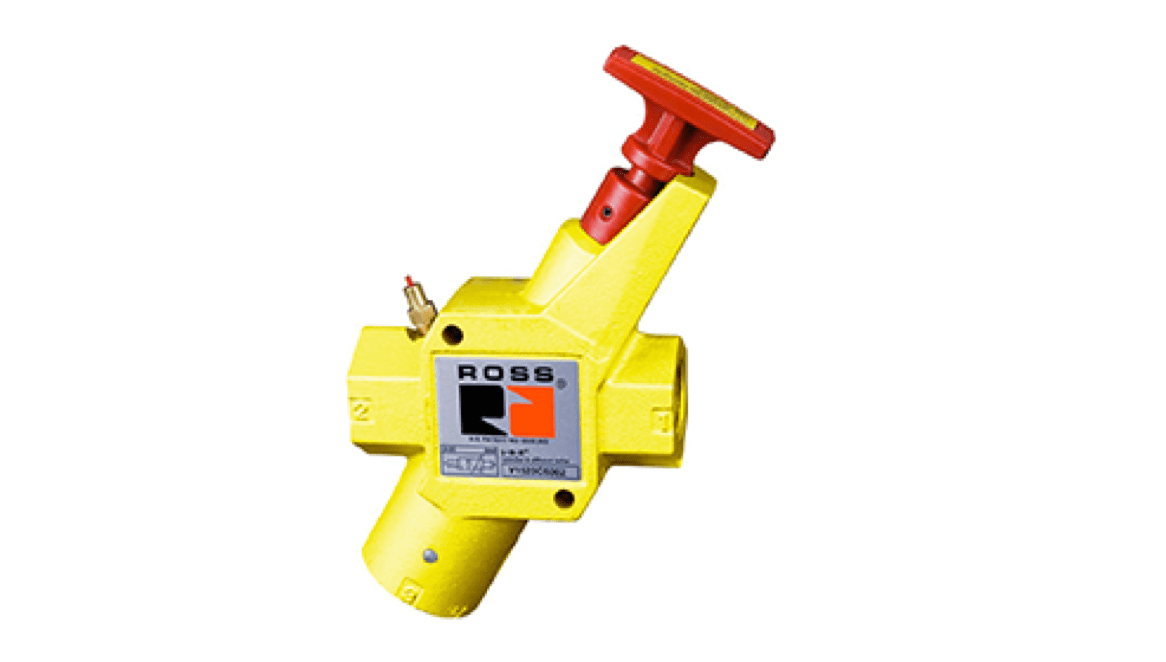
Manual Lockout Valve
- High flow rapid exhaust
- Depressurization Visualization Gauge (Optional)
- Soft Start (EEZ-ON®) (Optional)
- 316 stainless steel specification (Optional)
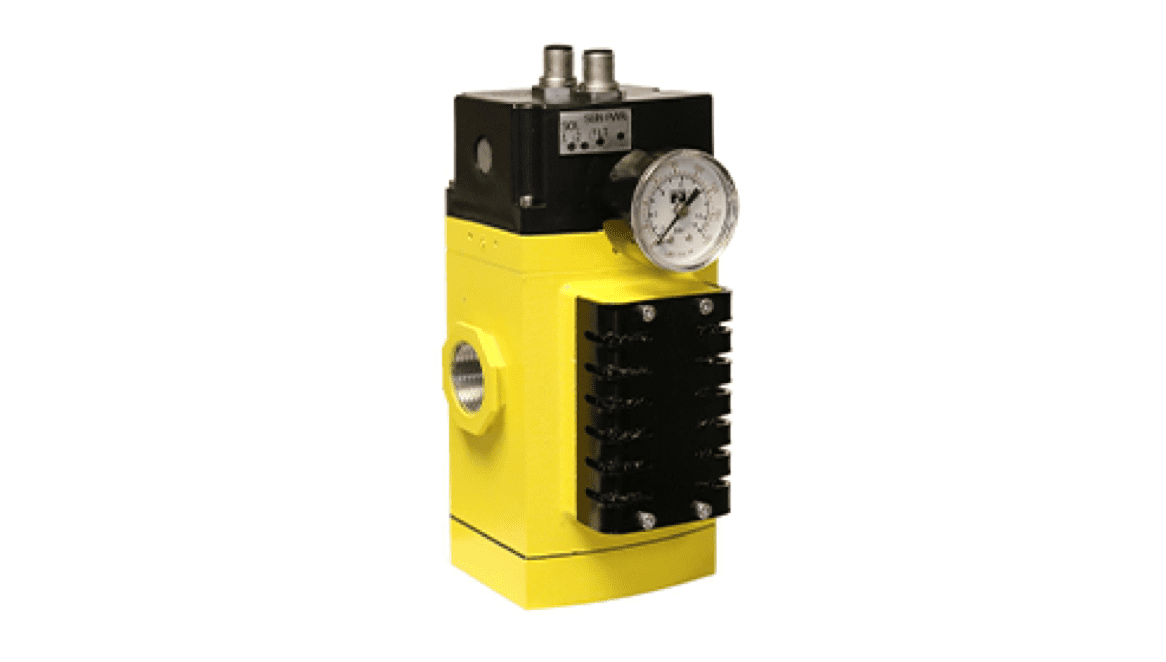
Safety Shut-off/Exhaust Valve
- 3/2 redundant valve
- Cat. 4 PLe
- SIL3
- Soft Start (EEZ-ON®) (Optional)
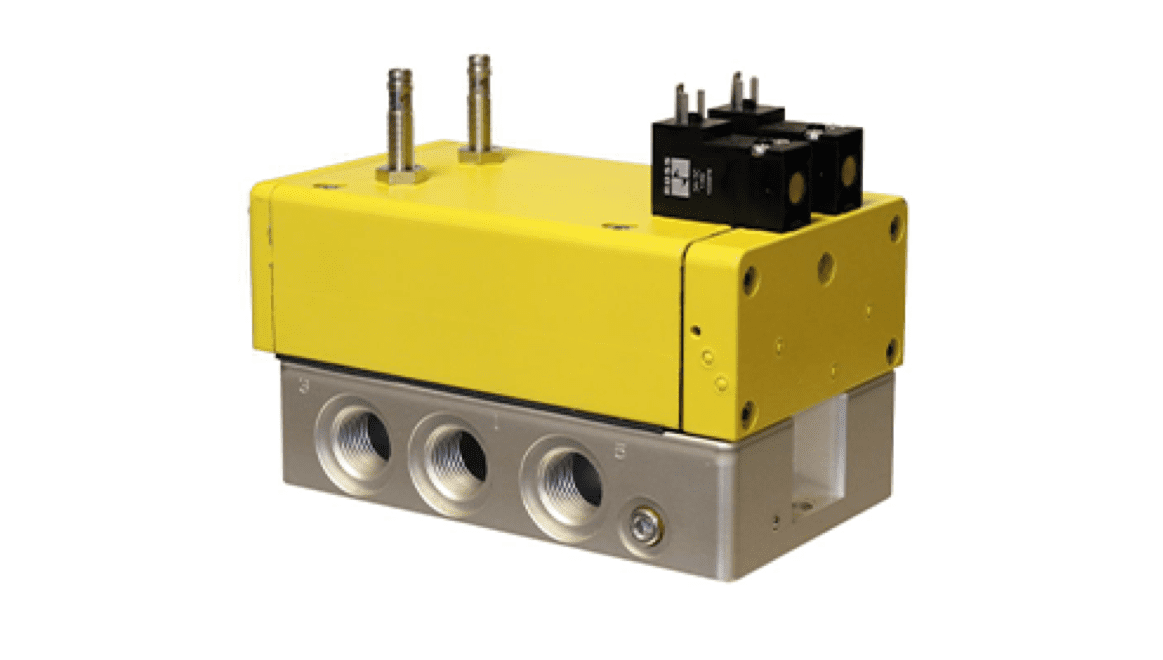
Safety Cylinder Control Valve
- 5/2 redundant valve
- Cat. 4 PLe
- SIL3
- Base mount specification
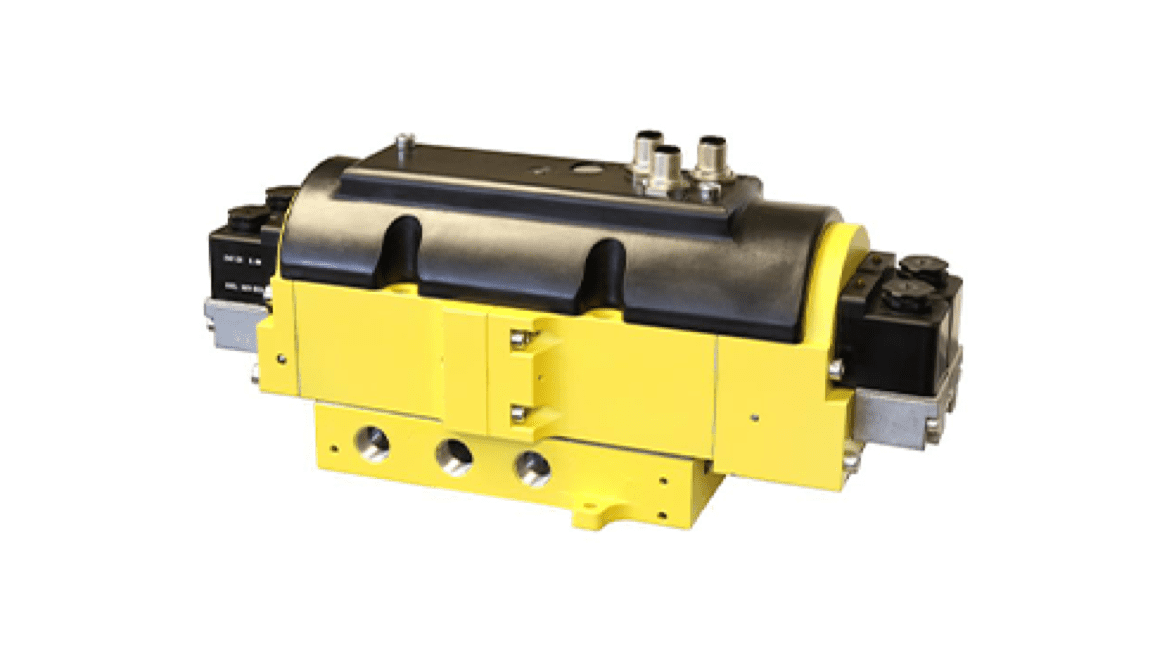
Safety Fall Prevention Valve
- 4/3 redundant valves
- Safety cylinder stop
- Cat. 4 PLe
- Poppet valve structure
Click here for the concept and countermeasures of risk assessment.
Click here for safety categories and performance levels.
Contact Our Team
ROSS employs a powerful team of experts with vast experience in fluid power able to help you find a solution for your safety goals. Whether it be a custom solution, a current product, application, or safety course, ROSS is here to provide just what you need with your business specifications in mind.